-
Video: Rotamat coating machines
-
-
-
-
Rotamat R 100
The principle
The work pieces are gently tumbling over each other in the rotating drum. The resulting intensive mixing effect evenly exposes the work pieces to the spay pattern of the spray gun at different angles – a pre-condition for an even coating thickness.
The special drum shape and the adjustable rotary speed ensure an optimum tumbling and mixing of the work pieces. The drum inclination is infinitely adjustable within a certain angle and can, thus, be precisely adjusted to different work piece shapes. The ideal angle of inclination for the various coating processes is determined by processing trials and then stored in the machine controls.
Different drum sizes for different part volumes are available. Exchanging one drum with another is easy and requires very little time. This allows adapting the Rotamat quickly to different batch sizes or coating processes. If required, the inside of the drums can be lined with a 3S-coating. In addition, the inside of the cover and the drum housing can be coated with an anti-adhesion material.
Once the coating process is completed, the drum is mechanically tilted downward for gently discharging the finished work pieces, which are now ready for the next production step.
Homogeneous application of the coating material
An automatic spraying systems evenly applies the coating material onto the work pieces gently tumbling in the rotating drum. If requested, the machines can be equipped with two spraying systems. This is advised, if work pieces must be coated sequentially with two different materials like base and topcoat or primer and cover).
The automatic spraying systems, type HVLP, used in the Rotamat coaters produce very little spray mist resulting in a minimum of overspray.
A window in the drum cover allows the operator to visually inspect the coating process. The inside of the drum is equipped with explosion protected LED lights.
Optimum temperature
During the coating process pre-heated, filtered air is injected into the rotating drum to heat the work pieces to a pre-set temperature, which is precisely adapted to different work piece types and materials as well as different coating materials. Throughout the process the work piece temperature is monitored by an IR sensor, and the inlet air temperature is adjusted as required.
This results in a highly homogeneous, evenly coated surface, creating an intensive bond between the coating material and the work piece surface. The coating material already dries during the actual spraying process. Post process drying in a separate oven is no longer required.
Repeatable coating results
An industrial PC monitors and controls the entire process.
The integrated recipe administration stores all process parameters created for the different applications and allows quick access to the different recipes. These include, for example, work piece quantities, inlet air temperature, drum speed (RPM), spraying volume and spraying pattern of the automatic spraying system.
The result: A stable process with absolutely repeatable, perfect coating results.
The intuitive process visualization, simple operation of the touch panel and process and control functions makes working with the Rotamat very easy.
Eco-friendly operation
Each Rotamat coater is equipped with a 4-stage exhaust air filter system including a Papp labyrinth filter, a filter mat and pocket filters.
The rotating drum is sealed allowing the work pieces to be processed under a slight negative pressure. This prevents hazardous volatile materials from escaping into the environment.
Application Images
-
Decorative coating of wood
-
Decorative coating of wood
-
Decorative coating of wood
-
Corrosion protection for screws
-
Decorative coating of plastic parts
-
Decorative coating of plastic parts
-
Decorative coating of metal parts
-
Decorative coating of metal parts
-
Decorative coating of plastic parts
-
Coating metal parts with adhesive
-
Coating rubber parts with lubricant
-
Coating metal parts with adhesive
-
lubricant coating of sealing rings
Technical Specifications
R 100 | |
---|---|
Power (kVA) | 19 |
Power supply (V/Hz) | 400/50 |
Compressed air, dry, oil-free (in bar) | 6 |
| |
Drum (mm) | 550/600/700/800/850 |
Filling weight max. (kg) / Filling volume max. (l) | 100/160 |
Speed of drum (RPM) | 2...30 |
| |
Transporting capacity max. (m³/h) | <160 |
Heating capacity (kW) | 9 |
Increase of temperature max. (K) | 130 |
| |
Transporting capacity max. (m³/h) | <200 |
Filtration | 4-stage F6 |
EX marking (as per type plate) | Ex II 1/3/-G Ex IIB T3 Ga/Gc/-X |
Max. infeed of solvent (g/h) | 1,000 |
Dimensions R 100
Measurement table
R 100 | |
---|---|
A (depth) | 2,550 |
B (width) | 2,070 |
C (height) | 2,140 |
Dimensions in mm |
Downloads
Links
Sales Manager
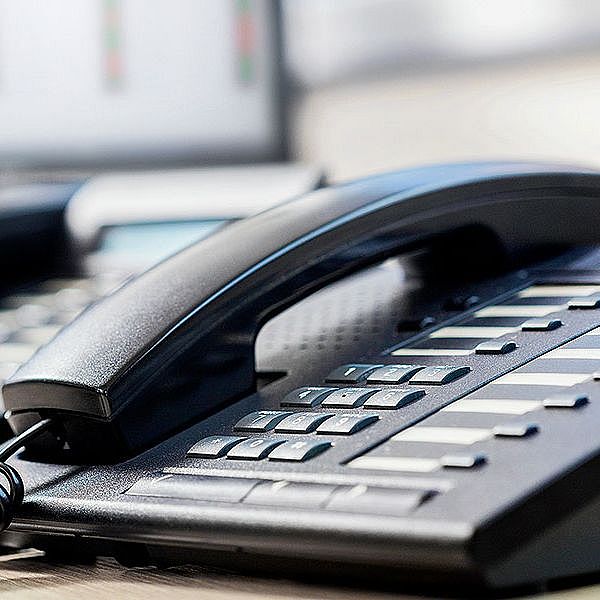