What is vibratory finishing and how does it work?
Mass finishing, also known as barrel finishing, is based on a natural principle. Similar to how sand and water grind coarse rocks into smooth pebbles in nature, modern production technology gives workpieces the desired surface. By using specialised machines, abrasives, compounds and water, we achieve precise and desired surface finishes. Compared to manual processing methods, vibratory finishing offers numerous advantages: It enables reproducible results and more economical manufacturing processes.
Our vibratory finishing machines at a glanc
Walther Trowal offers a wide range of advanced vibratory finishing machines. From circular vibrators to trough vibrators and customised systems - our machines meet the requirements of modern production environments and offer high adaptability to different materials and processing objectives. Discover our product overview for detailed information.
The application areas of mass finishing technology
Today, vibratory finishing is a widespread mechanical-chemical manufacturing process that is used in various areas of application, including:
- Deburring and rounding of edges: Vibratory finishing ensures clean and precise edges, free of burrs and sharp transitions.
- Smoothing and polishing: Fine tuning of the sanding process allows surfaces to be polished to a mirror finish.
- Cleaning and degreasing: In addition to surface finishing, vibratory finishing also enables effective cleaning and degreasing of workpieces.
- Descaling and derusting: Even stubborn oxidation layers such as scale and rust can be efficiently removed using mass finishing technology.
Vibratory finishing is suitable for workpieces made from all common metals and metal alloys. The technology can also be used for moulded parts made of rubber, plastic or ceramics, making it a versatile solution for a wide range of industries. By using mass finishing technology in your production, you can not only increase the quality and aesthetics of your products, but also significantly improve the efficiency of your manufacturing processes. Discover how mass finishing technology can also support your production goals.
The advantages of the mass finishing process at Walther Trowal
The mass finishing process offers numerous advantages over traditional machining methods. It is particularly efficient when machining complex or delicate parts and can process several workpieces simultaneously without monitoring. Here are some of the advantages that vibratory finishing offers:
- Uniform machining: All surfaces of the workpiece are treated evenly.
- Time efficiency: Simultaneous processing of several parts saves time.
- Flexibility: Different media and intensities allow for a wide range of finishes.
- Cost efficiency: Reduces manual labour and increases throughput times.
Surface finishing at Walther Trowal
In addition to mass finishing machines and mass finishing processes, Walther Trowal offers comprehensive solutions for surface finishing. From simple cleaning processes to highly specialised polishing processes, we ensure that your components achieve the desired surface quality. Our experts work closely with you to develop the best possible solution for your specific requirements.
Contact us for a personalised consultation
Are you interested in our vibratory finishing machines or do you need personalised advice on the mass finishing process and surface finishing? Our area sales managers will be happy to discuss your specific requirements and find the perfect solution for you. Contact us today and put your trust in Walther Trowal - your expert for mass finishing technology. We look forward to supporting you!
WALTHER TROWAL LTD. SALES DIVISION
Matrix Point
120 Devon Street
Saltley
Birmingham
B7 4SL
United Kingdom
Tel.: +44 121 270 4555
Fax: +44 121 270 4567
E-mail
Your contact partner
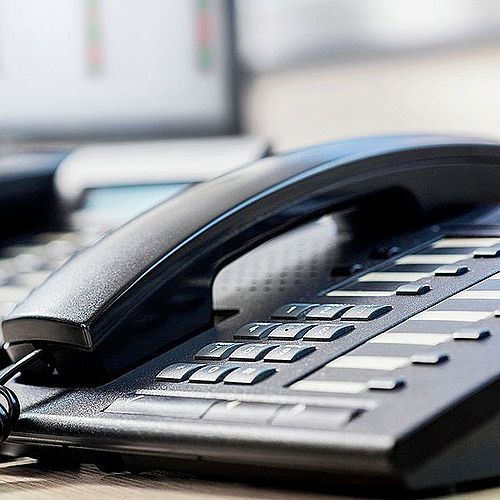
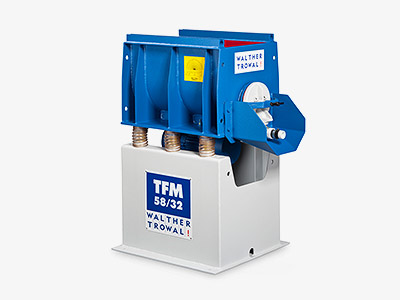
Trough vibrators
If your workpieces are too large for circular vibrators, simply process them individually in the trough. Sensitive parts can be secured or processed in separate chambers.
to overview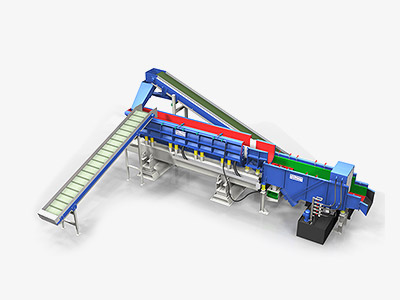
Continuous units
Our continuous units can be installed to continuously process your workpieces in the production process. The individual parts are added to the mass finishing machine in cycles, without interrupting the process.
to overviewquick entrance
AV unit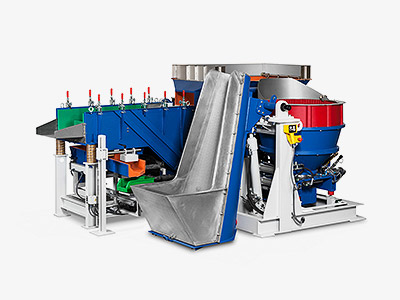
Centrifugal disc finishing units
Centrifugal disc finishing units have an abrasive action that is ten times stronger than that of circular vibrators. This helps remove heavy burrs and round off edges on small and medium workpieces.
to overview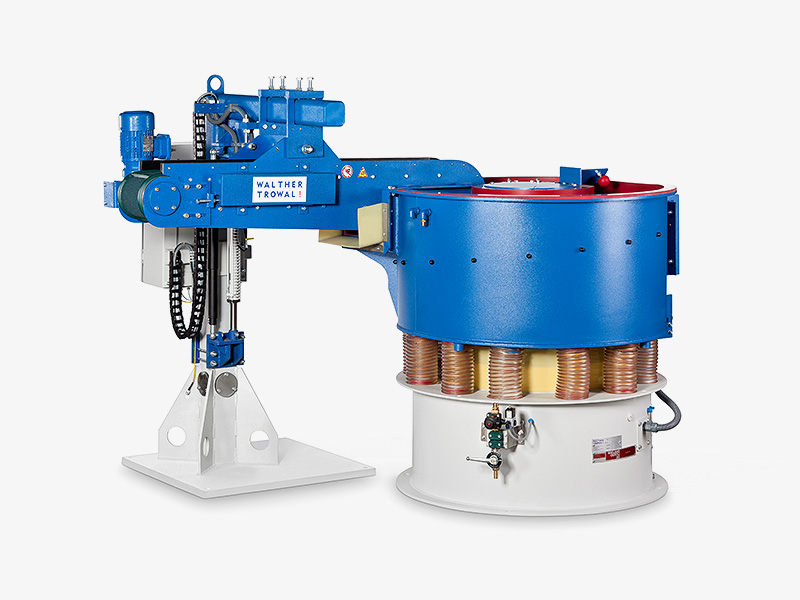
Circular vibrators
From deburring and rounding to high-gloss polishing, circular vibrators can be used anywhere.
to overview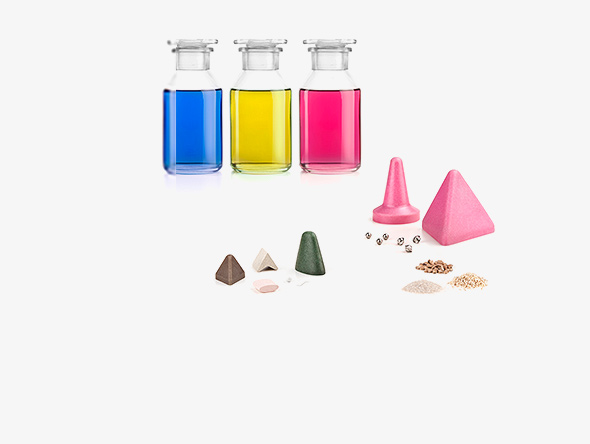
Consumables for mass finishing machines
The right combination of process media can ensure the perfect processing results. Ceramic and plastic abrasive media, combined with compounds and special media, create the ideal surface.
to overview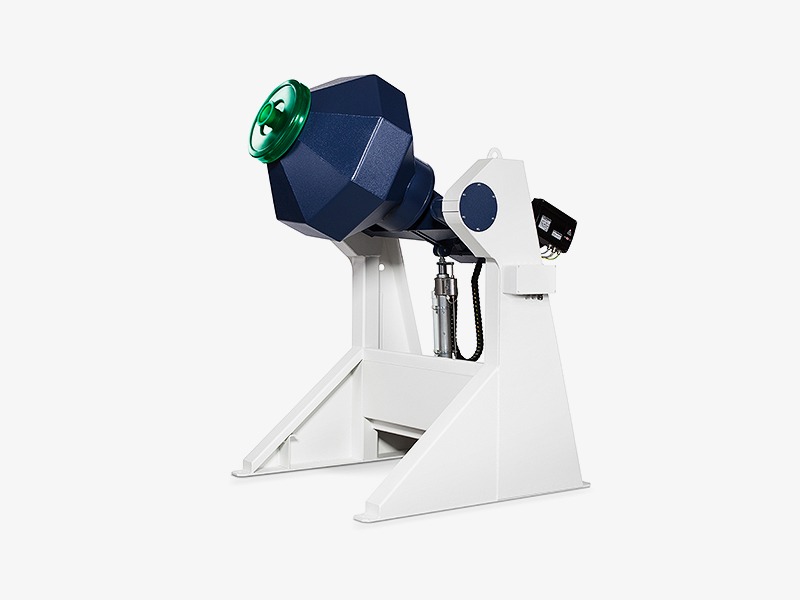
Drums and rotating barrels
Drums and rotating barrels are the cost-effective solution for processing small workpieces – such as those in precision mechanics – in small and medium batch sizes. They are also suitable for fine finishing and polishing.
to overview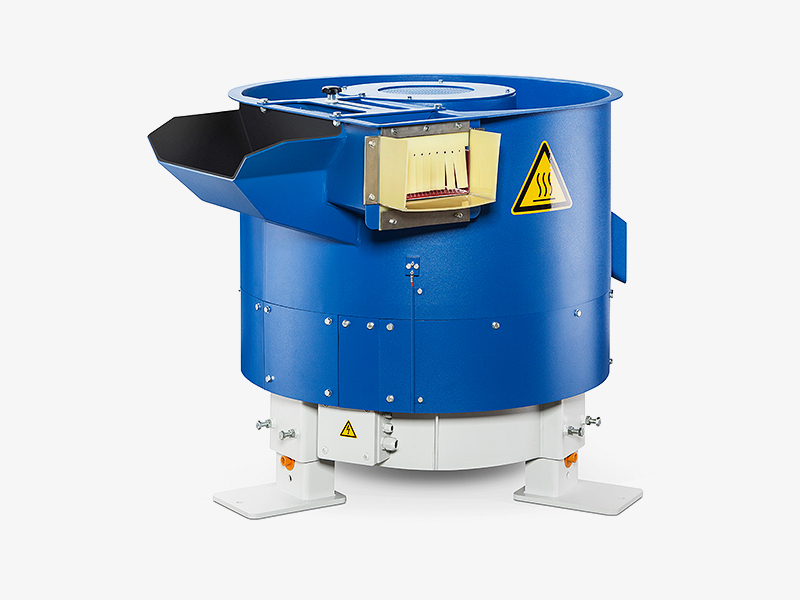
Dryers
After mass finishing, workpieces are generally wet or moist and must be dried. This is done using either a heated drying medium or hot air, depending on your individual needs.
to overview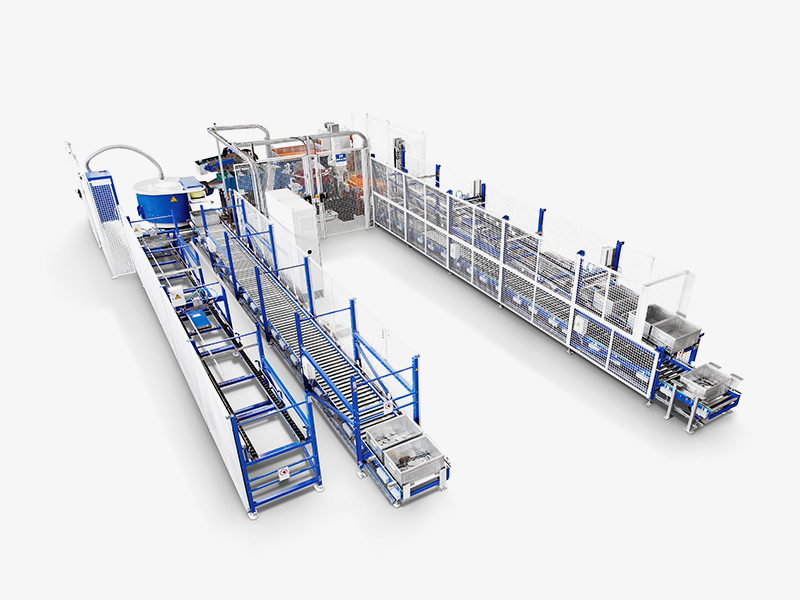
Accessories
Our wide range of accessories can help you adjust circular vibrators, trough vibrators, continuous units and all other processing systems to your individual requirements, and help you improve your processes.
to overview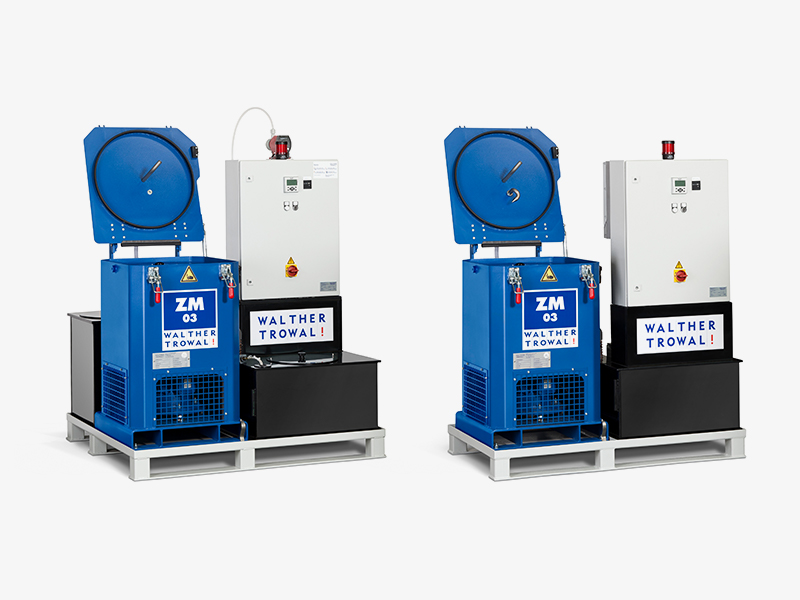
Process water: Innovative solutions for surface technology
Effective and efficient, reusing process water (a mixture of water and compound) and feeding it back into circulation during mass finishing can help you both save costs and protect the environment.
to overview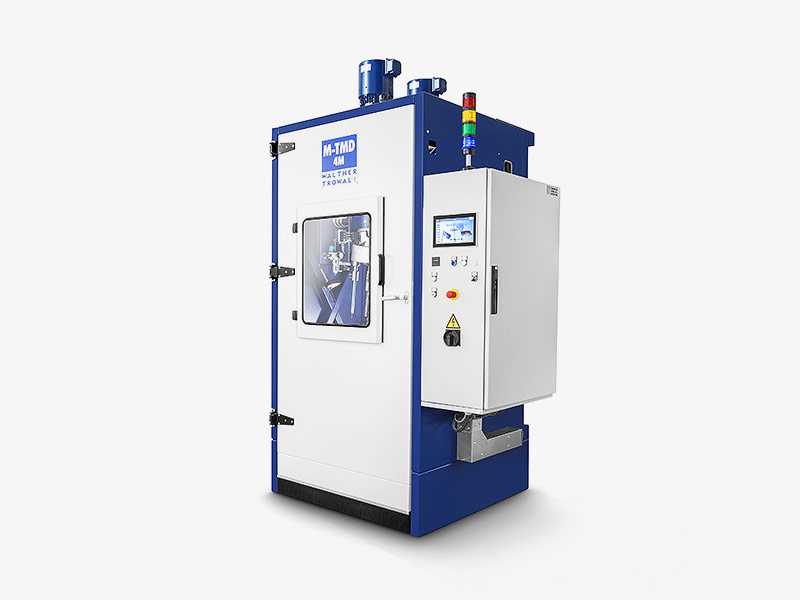
Drag finishers
High-value, delicate work pieces with complex shapes or work pieces made from tough, difficult to machine materials are mounted to special fixtures and dragged through a stationary bed of grinding or polishing media. Since the work pieces never touch each other during the process, they cannot scratch or nick each other.
to overview